Influence of ageing and radiation on ductile fracture in the DBT temperature region
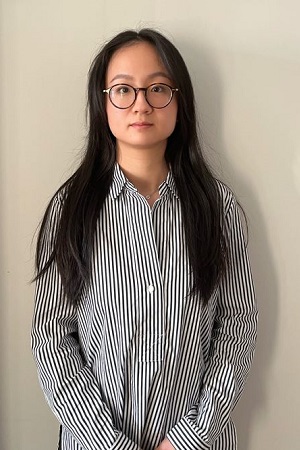
Research host
KTH Royal Institute of Technology, Department of Engineering Mechanics, Unit of Solid Mechanics
Research done by doctoral student
Shuyue Wang
Main supervisor
Prof. Jonas Faleskog
Co-supervisor
Adj. Prof. Pål Efsing
Formal project start
2020-08-17
Expected time of completion
2025-06-25
Discipline
Solid Mechanics
Keywords
Ductile fracture, length scales, ageing degradation, long-term structural integrity, material inhomogeneities
Motivation
Ductile fracture involves a significant amount of plastic dissipation which increases the resistance of a material to withstand the growth of existing defects to failure. However, long-term operation at elevated temperatures may lead to a degradation of this resistance and consequently a less ductile material. If the material also is subjected to a hostile environment as found in nuclear power plants, this degradation can be accelerated.
The structural integrity of the large pressure-retaining component is vital to the continued operation of the Nuclear Power Plants beyond the initially assumed lifetime. Currently, 6 plants in Sweden are planning for Long Term Operation, LTO, extending the life beyond the 40 years lifetime assumed in many of the original analyses. The process of LTO is a common tool to extend the lifetime of the plants utilized in most Nuclear operating countries. Including an assessment of all systems, structures, and components relevant to, or affecting, nuclear safety.
The objective of this study is to understand the influence of time-dependent ageing and degradation mechanisms on the ductile behaviour of low alloy steels at temperatures above the Ductile to Brittle transition temperature, DBTT. By understanding limitations and conservatisms, a sound basis
for the assessment of the structural integrity can be obtained and measured to improve and visualize the nuclear safety of the operating plants from a LTO perspective, in both a regulatory and operations perspective.
Specifically, the possible influence of microstructural entities and defects on the scale ranging from about ten nanometers to one millimetre, combined with an overall change in plastic flow properties on ductile fracture, will be investigated. The work involves comprehensive literature studies in the field, development of micromechanical-based damage models for ductile fracture and failure in general geometries suitable for numerical analysis by the finite element method, and validation of experimental results.
Key findings thus far
A non-local damage mechanics model for ductile fracture and failure has been developed that comprises two material length scales. One is associated with shear failure and the other with high constraint fracture in mode I crack. The model has been implemented in a material routine for finite element analysis to predict material failure in general geometries. A comprehensive study on a large set of test specimens reveals the model can capture and well describe the evolution of damage in high constraint tension dominated geometries to geometries failing by shear localization. A paper to be submitted to a scientific journal is under revision.
Currently, a set of experiments are carried out on a ductile nuclear pressure vessel steel to calibrate and validate the model. The aim is to establish an appropriate framework for analysis of the aged alloy steel used in the large pressure-retaining component in Nuclear Power Plants.
Publications from this project
Wang, S. & Faleskog, J. (2022, April 4–6). A regularized GTN model separating the length scales associated with shear and flat dimple rupture [Conference session]. APA 2022 18th European Mechanics of Materials Conference (EMMC18), University of Oxford, United Kingdom.
Wang, S. & Faleskog, J. (2022, June 15–16). A regularized GTN model separating the length scales associated with shear and flat dimple rupture [Conference session]. APA 2022 27th Swedish Mechanics Days (SMD2022), Luleå University of Technology, Sweden.